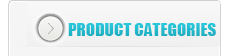

The production process of polypropylene FDY yarn itself is a precise chemical dance. The FDY process, whose full name is "Fully Drawn Filament", converts polypropylene raw materials into continuous fine filaments through melt spinning technology. During this process, the delicate balance between temperature control, tensile force and cooling rate determines the quality characteristics of the final fiber. Unlike traditional spinning processes, FDY technology highly orientations the fiber molecular chains and increases the crystallinity, thereby endowing polypropylene filament with excellent strength and dimensional stability. Behind this seemingly simple physical change lies the unremitting pursuit of countless engineers for the performance limits of materials.
The remarkable feature of polypropylene FDY yarn lies in its excellent physical properties. It is as light as a feather yet extremely tough, with excellent tensile strength and wear resistance, which enables the fabric made from it to withstand repeated use and washing. Meanwhile, the hydrophobic property of polypropylene fibers gives them the advantage of rapid drying, making them shine in the fields of sportswear and outdoor products. Even more astonishingly, the density of polypropylene FDY filament is less than that of water, which provides an ideal material for water rescue equipment. These performance advantages are not accidental but the result of meticulous design and optimization of the molecular structure of polypropylene by materials scientists.
In today's era that emphasizes environmental protection, polypropylene FDY yarn has demonstrated a rare environmental friendliness among synthetic fibers. Its raw material, polypropylene, is derived from petroleum by-products. The production process has relatively low energy consumption and does not involve the use of harmful chemicals. What is even more valuable is that polypropylene fibers can be recycled and reused, providing the possibility for a circular economy in the textile industry. Compared with other synthetic fibers, polypropylene has a relatively small impact on the environment after being discarded, making it an important choice for the fast fashion industry in its pursuit of sustainable development. Of course, this does not mean that polypropylene is perfect. How to further improve its biodegradability remains a challenge for researchers.
From the minute details of daily life to special applications in professional fields, the application map of polypropylene FDY yarn is constantly expanding. In the field of clothing, it is often blended with other fibers to endow the fabric with stiffness and durability. In household items, it appears in the form of carpets, curtains, etc., demonstrating excellent anti-stain performance. In the medical field, polypropylene non-woven fabric has become an ideal choice for disposable protective products. In industrial applications, its chemical resistance makes it an excellent raw material for filter materials and ropes. It is particularly worth mentioning that the application of polypropylene FDY filament in automotive interiors is becoming increasingly widespread. Its UV resistance and weather resistance provide a long-lasting and comfortable environment for drivers and passengers.